Our factory

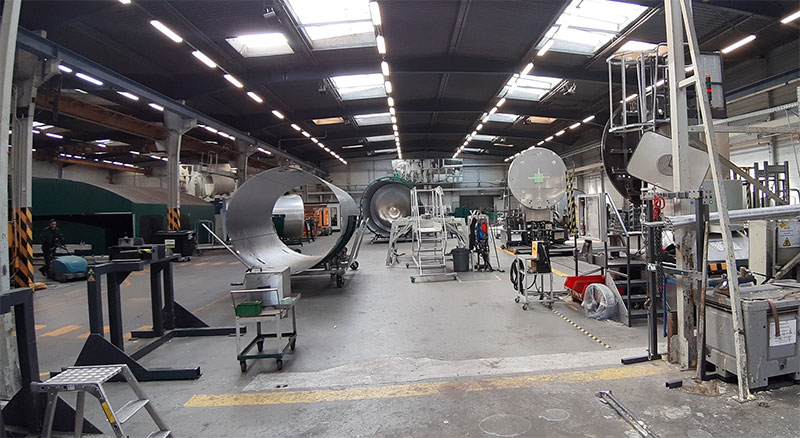
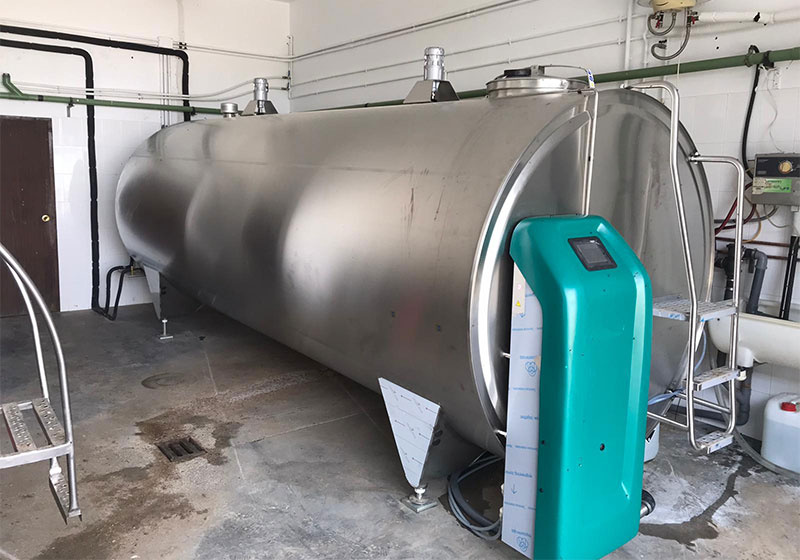
- cutting, forming and producing small capacity tanks
- medium and large capacities production
- all equipment assembly
The highest Quality standards

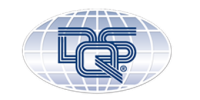
ISO 9001
ISO 9001 certification focuses on the ability of our management system to guarantee the quality of our products and customer satisfaction. Certification covers all of our work steps, from receiving raw materials to taking corrective action in light of the feedback received.
Click here to see our certificate.
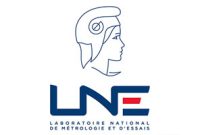
LNE
The National Laboratory of Metrology and Testing (LNE) intervenes to ensure the accuracy and compliance of our metrology tools. Our tanks are measured and therefore considered as measuring tools, they have a certification granted by the LNE laboratory.
Click here to see our certificate.
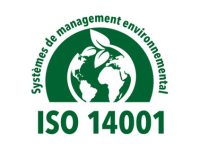
ISO 14001 : 2015
The environmental impact of our industrial activity is at the heart of our priorities.
JAPY TECH is very committed and respectful, this translates, among other things, into :
- waste control and reduction
- water use control
Our commitment is confirmed by obtaining the certification ISO 14001: 2015.
Click here to see our certificate.
EN standard
As one of the oldest existing manufacturers, JAPY TECH helped draft the EN 13732 standard, the purpose of which is the cooling of bulk milk on the farm.
This standard sets out the minimum requirements for thermal, washing, acoustics and milk agitation performance.
JAPY TECH is an integral part of the Standards Committee
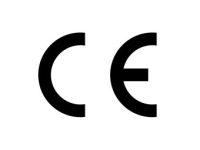
European compliance
The CE label attests our compliance with the European directives applicable to all our products.
Click here to see our certificate.
R&D Department

Innovation has always been an important part of JAPY TECH’s strategy. Developments such as high-thermal exchange evaporators, digitalization of orders or improved tank washing have helped to increase food safety and the quality of milk collected in Japy tanks.
Our research and development department has sharp skills on all dimensions that make a tank of good quality: stainless steel work, refrigeration condensing unit design, control electronics…
Two thermoregulated test rooms allow the qualification of all these developments and the validation of the mathematical models used in the design of the tanks.
The fruits of our research are protected by several patents, such as the agitation of milk in our silos, the analysis of cooling speed or the security of remote access.
This ensures that we meet the highest levels of customer demand and enables them to always benefit from the latest technological advances.
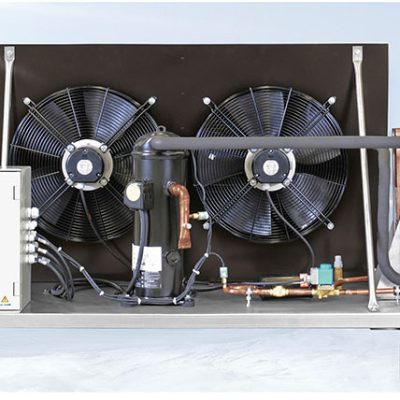
- Food security
- People’s safety
- To measure cold performance and thermal insulation
- The quality of washing
- The energy consumption
- The sound level
Our refrigeration systems are in compliance with the EN378 standard, which describes the rules for construction and testing to ensure the safety of people and the environment of refrigeration equipment.
Our wash controller ICool, on the other hand, meets the EN61000-6 standard, which guarantees electromagnetic compatibility in order to avoid disturbances on other electronic equipment.
All products meet the standards set by the EN60204-1 standard for electrical safety of equipment.